Types of Brazing: Definition, Principle, Applications, Advantages & Disadvantages
What is Brazing?
Brazing is a process of metal-joining in which two or more metal items are joined together by melting and flowing a filler metal into the joint, with the filler metal having a lower melting point than the joining metals.
The melting temperature of the filler material is about 600°c, but lower than the melting temperature of the adjoining metal. The filler metal is dispersed amid the surfaces by capillary action.
Brazing is different from welding as it doesn’t involve melting the work pieces and from soldering in using high temperatures.
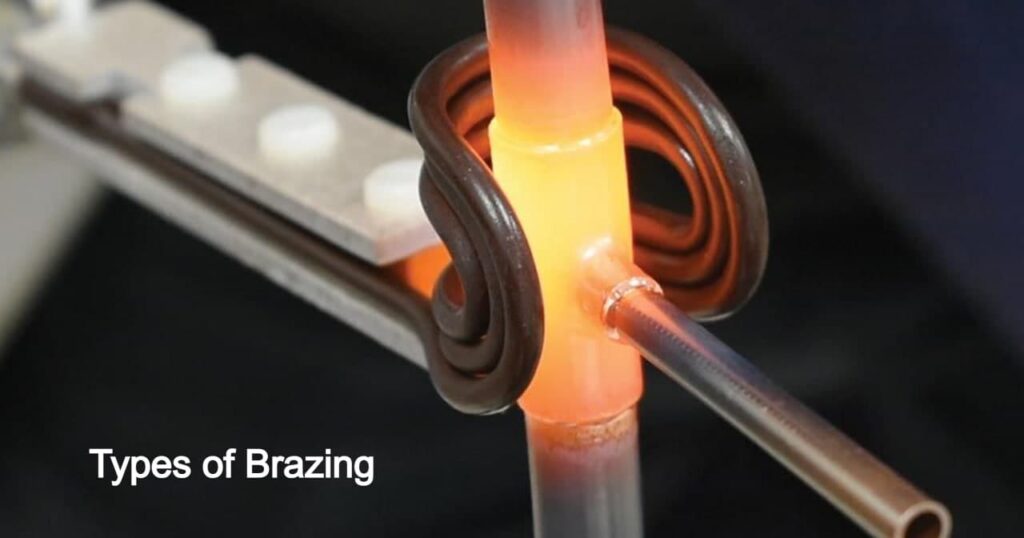
Principle of brazing:
The surfaces to be joined are cleaned to remove oxides and contaminants. After cleaning, they are coated with flux or a material capable of dissolving solid metal oxides present to prevent new oxidation. The joint area is then heated until the flux melts and cleans the base metal. The base metal is protected against further oxidation by the liquid flux layer.
Brazing filler metal is made to be melted at some point on the surface of the joint area. Capillary attraction is much higher between the base and filler materials than that between the base metal and flux. Hence, the flux is removed by the filler metal. The joint, upon cooling at room temperature, will be filled with solid filler metal. The solid flux will be found on the surface of the joint.
Types of Brazing
- Torch brazing
- Furnace brazing
- Silver brazing
- Brake welding
- Induction Brazing
- Resistance Brazing
- Cast iron welding
- Vacuum brazing
- Dip brazing
- Infrared brazing
Torch Brazing:
Torch brazing is the most commonly used method in mechanized brazing. It is commonly used for smaller production runs or one assembly.This type of brazing is performed by using a heated gas torch set to the proper required composition, and an appropriate flux. This depends on the requirement of temperature and heat. The fuel gas (acetylene, propane, etc.) may be burned with air, compressed air, or oxygen.
Brazing filler metal may be placed in advance at the joint in the forms of rings, washers, strips, slugs, or powder, or it may be fed from hand-held filler metal in the form of wire and rod. In any case, proper cleaning and fluxing are essentially required.
There are three main types of the torch brazing:
- Manual torch brazing
- Machine torch brazing
- Automatic torch brazing
Furnace Brazing:
Furnace brazing is a semi-automatic process which is widely used in industrial brazing operations due to its flexibility to mass production and unskilled labour. One of the main advantages of furnace brazing is that it can produce a large number of small parts very easily that can toothed or self-detected. It includes a controlled heat cycle.
Furnace brazing is used widely where the parts to be brazed can be assembled with the brazing filler metal placed in advance or near the joint in the form of wire, foil, filings, powder, paste, etc.
A large volume of furnace brazing is performed in vacuum, which prevents oxidation and mostly eliminates the need for flux.
Silver Brazing:
Silver brazing also known as “hard soldering” or “silver soldering,” is a low-temperature brazing process. It includes rods having melting points ranging from 1145 to 1650ºF (i.e. 618 to 899ºC).
The silver alloys based filler metalcontains many different percentages of silver and other metals, such as copper, zinc, and cadmium.
The strength of a joint made by this process depends on a thin film of silver brazing filler metal.They are used for joining all ferrous and non-ferrous metals except aluminium, magnesium, and other metals which have a too low melting point.
Brake welding:
Brake welding uses a bronze or brass filler rod coated with flux to attach the steel workpiece. The equipment required for braze welding is basically the same as the equipment’sin brazing.
Acetylene or methyl acetylene-propylene (MAP) gas fuel is commonly used since brake welding usually requires more heat.
Induction Brazing:
The heat required in the process ofbrazing metals is obtained from a high frequency electric current consisting of a motor-generator, resonant spark gap, and vacuum tube oscillator. The current is induced without any contact with parts. Filler metal is normally pre-placed.
The equipment consists of tongs or clamps (preferably water cooled) with the electrodes attached at the end of each arm.
Resistance Brazing:
The resistance to the flow of an electric current through the electrodes and the joint to be brazed delivers the heat necessary for resistance brazing.The parts comprising the joint constitutes a part of the electric circuit. The brazing filler metal is pre-placed or face fed.Flux is employed except when an atmosphere is specially introduced to perform the same function.
The parts to be brazed are held between two electrodes, and essential pressure and current are applied. The pressure should be maintained until the joint solidifies.
Cast iron welding:
Welding of cast iron is usually a brazing operation, in which mainly nickel filler rods are used, although true welding with cast iron rods is also possible.
The main purpose behind this process is to use electricity with copper to hold underground climate pipes warm in cold climates.
Vacuum Brazing:
Vacuum brazing is a material joining method that gives important benefits such as extremely clean, superior, flux-free brake joints of high integrity and strength. A uniform room temperature is maintained when heated in vacuum reducing residual stresses due to slow heating and cooling cycles.
This process is costly because it must be done inside a vacuum chamber vessel.
Dip Brazing:
Dip brazing is particularly suited to aluminium brazing because of the absence of air, thus preventing the formation of oxides.
There are two methods of dip brazing:
- Chemical bath dip brazing
- Molten metal bath dip brazing.
Chemical Bath Dip Brazing: In chemical bath dip brazing, the brazing filler metal is pre-placed and the assembly is immersed in molten salt bath.The salt bath usually provides the necessary protection from oxidation.
Molten metal bath dip brazing: In this type of dip brazing, the components are dipped into the molten filler metal bath enclosed in a vessel. A cover of flux should be maintained over the molten bath to prevent it from oxidation. This method is largely confined to brazing small parts, such as narrow strips of metals and wires.
Infrared Brazing:
The principal heating is done by using the invisible radiation.Heat sources or lamps which are capable of delivering up to 5000 watts of radiant energy are commercially available.Reflectors are used to concentrate the heat at the part.The assembly is then heated to a controlled temperature, indicated by thermocouples. The part is moved to platens for cooling after brazing is done.
Advantages of Brazing:
Following are the advantages of brazing:
- Dissimilar metals and parts having a thin section can be easily brazed.
- Brazing protects the base metal from metallurgical damage.
- Greater strengthof joint can be obtained by brazing.
- Properly brazed joints are pressure tight.
- It is a quick and economical process.
- Lesser amount of heat is required than for welding.
Disadvantages of Brazing:
The disadvantages of brazing are as follows:
- Due to the soft filler material, the joint strength is less compared to a welded joint.
- The brazed joints can be destroyed under high temperatures.
- In Industrial setting, brazed joints need high-metal cleaning.
- The joint colour is usually different from the base metal.
Applications of Brazing:
Following are the applications of brazing:
- Used in vacuum interrupters.
- It is used in transport applications.
- Used in constructions.
- It is helpful in medical equipment.
- Used in art and jewellery ornaments.