Types of Extrusion Process: Working, Advantages & Disadvantages
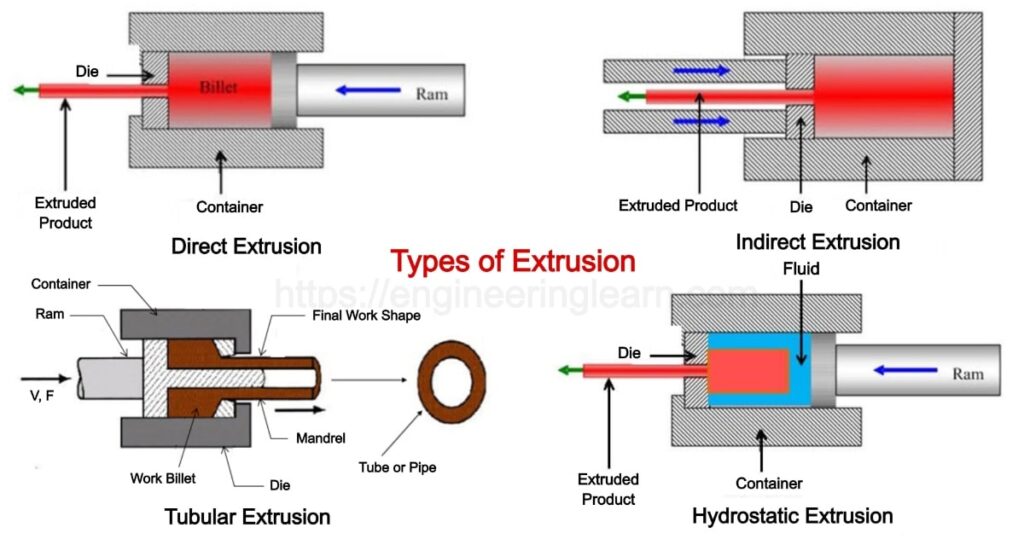
What is Extrusion?
Types of Extrusion Process: Working, Advantages & Disadvantages:- Extrusion is a high-volume metal forming manufacturing process in which the plastic or the granules of plastic is pressed by means of mechanical pressure into a die to get the desired shape. So, basically in the extrusion process, the melted material gets extruded throughout a die which is having a desired shape or opening.
This process is widely used in pipes and tube manufacturing. The force used to extrude the material is compressive in nature. This differentiates it from the drawing process in which tensile force is used. A basic example of the extrusion process is squeezing toothpaste from a toothpaste tube.
Working of Extrusion Process
In the extrusion process cylinder which is having a rotating screw is used to feed the plastic into the die, that these plastics are heated by an external source so it gets heated gradually and melted and then pressed against a die which is having a suitable opening of the desired shape. So, when the particular molten plastic is forced against that die with and then material comes out which having the exact shape of that particular die or the cross-section.
Extrusion Process in there are mainly three zones
1. Feed Zone
Inside the feed zone there is a hopper which is a gravity feed hopper. Inside this hopper plastic granules along with certain additives are added and this is fed into a barrel which is having a cylinder-piston assembly or it is having a screw assembly. This assembly crushes and pushes the plastic granules in a forward direction. This assembly is driven by a motor with the help of a gear reducer box.
2. Melting Zone
As the granules move forward, they pass through the melting zone. In this zone, these granules are heated by means of an external source. This is a controlled heating process because at higher temperatures unwanted hydrocarbons are generated which is avoided in this process. The temperature of this heating zone is sensed by the external thermocouples.
3. Melt-pumping Zone
In this zone, the melted plastic is fed inside the die by means of external force through the desired opening shape. The die opening is selected in such a way that the melted plastic reaches the die very quickly with high accuracy. At the end of this zone, a cutter is provided to cut off the material when they die gets filled. The pressure against the die is gradually increased up to a limit to avoid stress generation.
Types of Extrusion Process
- Direct extrusion
- Indirect extrusion
- Hydrostatic extrusion
- Tubular extrusion
1. Direct Extrusion: ( Types of Extrusion Process )
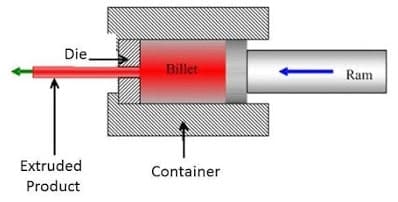
This is also known as forwarding extrusion. In this type of extrusion process, the material is forced to flow in the direction of force applied. A metal billet is placed on a chamber or a container. The billet is then forced through a die with the help of a ram. The die opening may be round or it may have various shapes depending on the desired profile of the product.
A Dummy block is provided to protect the tip of the ram, particularly in hot extrusion. In this process, a noteworthy amount of friction is present between the billet surface and the container walls, as the billet is forced to slip toward the die opening. Due to the friction, an increased ram force is required.
2. Indirect Extrusion: ( Types of Extrusion Process )
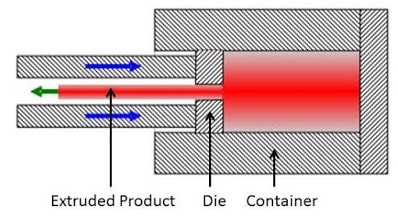
This is also known as backward extrusion. In this process, the metal flows towards the opposite direction of plunger movement. In this process, the die is mounted to the ram and not on the container. As the ram constricts the metal, it gushes through the die hole on the ram side which is in opposite direction to the motion of the ram. Because of the absence of relative motion between the billet and the container, no friction at the interface of both, and eventually lower ram force is required as compared to direct extrusion.
3. Hydrostatic Extrusion: ( Types of Extrusion Process )
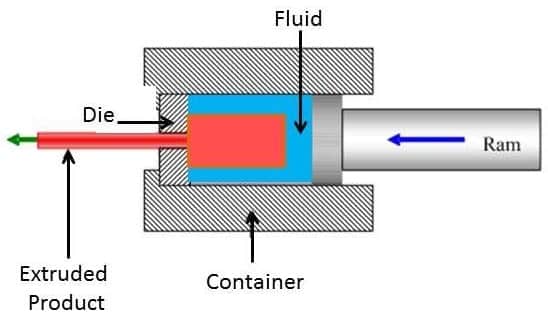
This process uses fluid to apply pressure on the billet. In this process, fluid is used to eliminate friction in the cylinder wall or plunger. The plunger exerts the force on the billet through the fluid by application of pressure. Normally vegetable oils are used as the fluid. This practice is used to solve leakage problem and uncontrolled speed of extrusion. This process is used for the extrusion of brittle material.
4. Tubular Extrusion: ( Types of Extrusion Process )
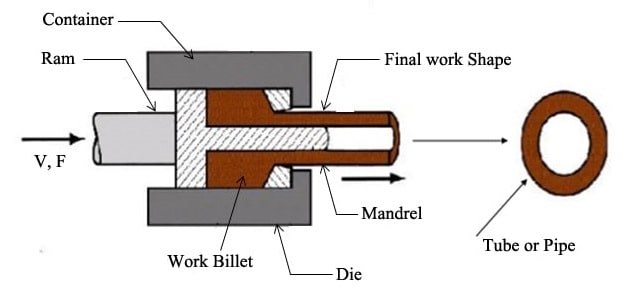
A tube is formed by pressing the extruded polymer through a circular die, cooling it in a water bath, and then cutting it or winding it up. This is mainly used in the production of railings, tubes, shafts.
According to the Working Temperature
1. Hot Extrusion
In this process, the process takes place above recrystallization temperature (50-60% of melting temperature).
Advantages of Hot Extrusion
• Low force required
• Ease of work in hot state
• The product is free from internal stresses
Disadvantages of Hot Extrusion
• Lower surface finish
• Scale formation
• Increase die wear
• High maintenance required
2. Cold Extrusion
In this process, the process takes place below the recrystallization temperature.
Advantages of Cold Extrusion
• No oxidation of the metal surface
• Greater surface finish
• High mechanical properties
Disadvantages of Cold Extrusion
• High force required
• Internal stresses generated
Application of Extrusion Process
• Extensively used in the production of tubes and hollow pipes
• In structural work aluminium extrusion is mainly used
• Production of frames, doors, window, etc
• Automobile industry
• Aerospace industry
• Widely used in plastic objects production
Advantages of Extrusion Process
• Complex shape can be extruded from the nonferrous metals.
• No draft
• Huge reduction in cross-section is possible
• Conversion from one product to another product requires only a single die change
• Good dimensional accuracy
• Flexibility in shapes
• Low running cost
• Best for mass production
• High extrusion ratio (ratio of billet cross-section to the extruded part)
• This can be applicable for brittle and ductile both
• High mechanical properties are achieved in the cold extrusion process
Disadvantages of Extrusion Process
• Cross-section must be uniform for the entire length of the product
• Size variation due to hot material an output (free expansion)
• High initial or setup cost
• High compressive force is required
• Not efficient for small production scale
Image Source :- Paulmurphyplastics, Quora