Solenoid Valve: Types, Parts, Operation, Working, Applications, Materials, Advantages & Disadvantages
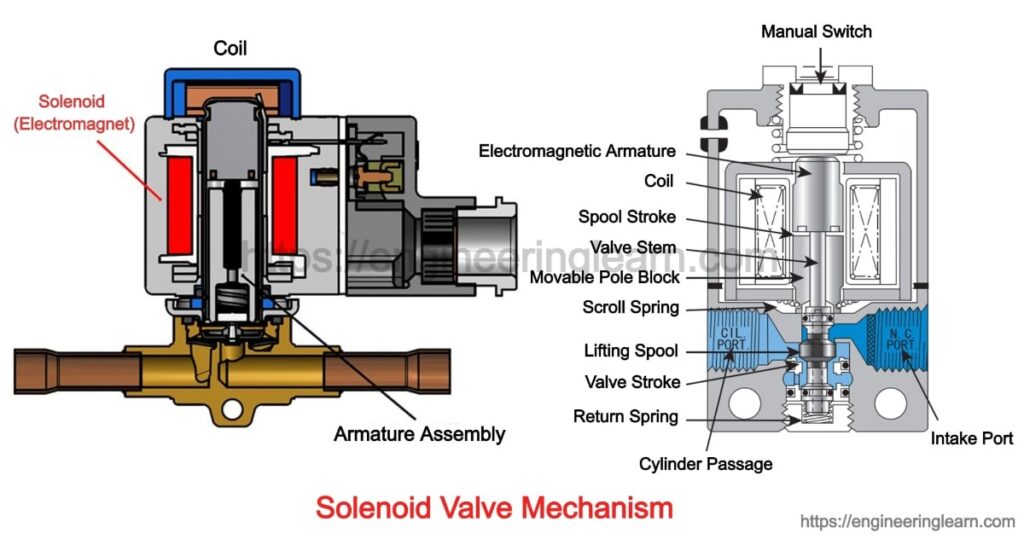
What is a Solenoid Valve?
Solenoid Valve: Types, Parts, Operation, Working, Applications, Materials, Advantages & Disadvantages :- These valves are electromechanically operated valves. Solenoid valves differ in properties of the electric current they use, strength of magnetic field they generate, mechanism which they use for controlling the fluid and fluid they control. The mechanism is different from the linear, plunger type actuator to the rocket actuators and pivoted armature actuators. For regulating the fluid, the valve use the design of two ports or it can use the design of three or more ports for switching flows between ports. On a manifold multiple solenoid, valves are placed together.
Invention of Solenoid Valves
ASCO Numatics in 1910 became the first company which developed and manufactured the solenoid valve. Solenoid valves are one of the most commonly used control elements in the fluidic logic. Their tasks are to release, dose, shut off, mix or distribute the fluids. Solenoid valves provide safe and fast switching, long service life, high reliability, compact design and low control power.
Operation of Solenoid Valves
There are various types of valves designs. Generally the valves have many fluid paths and ports. When solenoid is not energized and the valve is open then the valve is termed as normally open. When solenoid is not energized and the valve is closed then the valve is termed as normally closed. There are also more complicated designs like 3 – way valves. There are 3 ports in 3 – way valve, in which one port is connected to either of exhaust port or supply port.
These valves are characterized on the basis of operation. Limited force can be generated from small solenoid, if the generated force is sufficient to close and open the valve then only direct acting solenoid valve is possible.
Relationship between the fluid pressure, orifice area and the required solenoid force for the direct acting solenoid valve is
(Fs = PA =Pπd² / 4)
Where Fsis required solenoid force, P is the fluid pressure, A is the orifice area and d is the orifice diameter.
When large orifice and high pressure are encountered then high force is required and for generating those force solenoid valve design which is internally piloted may be possible. In such type of designs, for the generation of high valve force line pressure is used and the use of line pressure is controlled by a small solenoid.
Internally piloted valves are used when the fluid is water like in irrigation systems and dishwashers and the pressure might be 550kPa and orifice diameter might be 19mm.
The solenoid in few solenoid valves act directly on main valve while some other uses complete, small solenoid valve which is called as pilot for actuating a large valve.
And the solenoid valve which is combined with pneumatically actuated valve and packaged and sold as a single unit is known as solenoid valve.
Requirement of power in piloted valves for controlling is much lessbut are slower. For open and stay open piloted valves need full power supply at all the time while the full power requirement of a direct acting solenoid valve is for short period of time for opening and consumes very low power for staying open and they can operates in 5 milliseconds to 10 milliseconds while the piloted valve operation time depends on its size (generally 15 milliseconds to 150 milliseconds).
Working of Solenoid Valve
There are two main parts in solenoid valve: The Valve and the Solenoid.
The solenoid is applied to change the electrical energy into the mechanical energy which consequences to closing or opening of the valve mechanically. The solenoid valves can use rubber or metal seals and have electrical interface for allowing easy control. A spring is used for holding the valve closed or opened when the valve is not activated.