Torque Converter Working
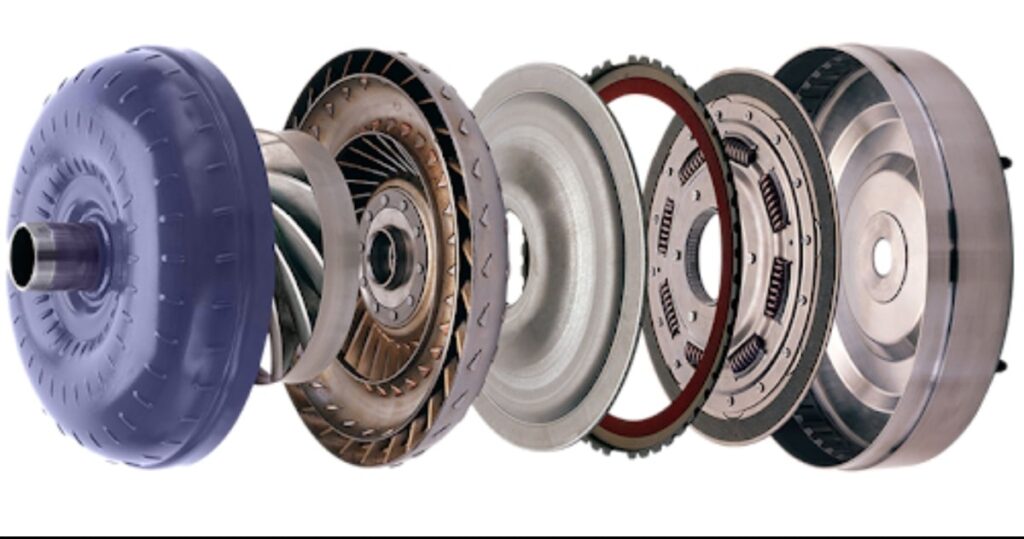
Torque Converter Working
Significance of torque converter work
In manual transmissions, an engine is connected to a transmission by way of a clutch. In absence of this connection, a car would not be able to come to a complete halt without damaging the engine. This is not the case in automatic cars. Automatic transmission cars use torque convertors for such purposes since cars with an automatic transmission have no clutch that disconnects the transmission from the engine. A vehicle’s torque converter acts the same as the clutch of a manual transmission vehicle. A torque converter, unlike a manual transmission vehicle, uses fluid to transmit power to the transmission, preventing the engine from stalling and allowing the transmission to change.
General Description
(A) Definition
A torque converter is an internal engine component that is shaped like a doughnut. It is directly attached between the engine and transmission. It is a type of fluid coupling device used in automatic transmission vehicles, which does the same work as the clutch in manual transmission vehicles, allowing the engine to spin almost independently of the transmission.
(B) Needof Torque convertor
Just like a manual transmission, cars with automatic transmissions also need a way to let the engine turn while its wheels and gears in transmission halt. For this purpose, manual transmission cars use a clutch, which completely disconnects the engine from the transmission. Since Automatic transmission cars do not have a transmission, they use a torque converter.
(C) Role of Torque convertor in vehicles
A torque converter is a fluid coupling device, which enables the engine to spin somewhat independently of the transmission. When the engine is turning slowly, such as idling at a red light, the amount of torque passed through the torque converter is very small; therefore, to keep the car still only a little pressure on the brake pedal is required.
If you step on the gas pedal while the car is still, you would have to press harder on the brake pedal in order to keep the car from moving. As you step more on the gas, the engine speeds up and starts pumping more fluid into the torque converter, which in turn causes more torque to be transmitted to the wheels.
Inside a torque convertor
(A) Construction
These devices are sealed units. Inside the torque converter, there are two series of opposite facing curved blades. There is a impeller (or fan) present which is connected to the engine. The impeller combined with the front cover forms the outer covering of the convertor. The other fan, or the turbine, is connected to the transmission input shaft. Any motion of the turbine will move the vehicle unless the transmission is in neutral or park.
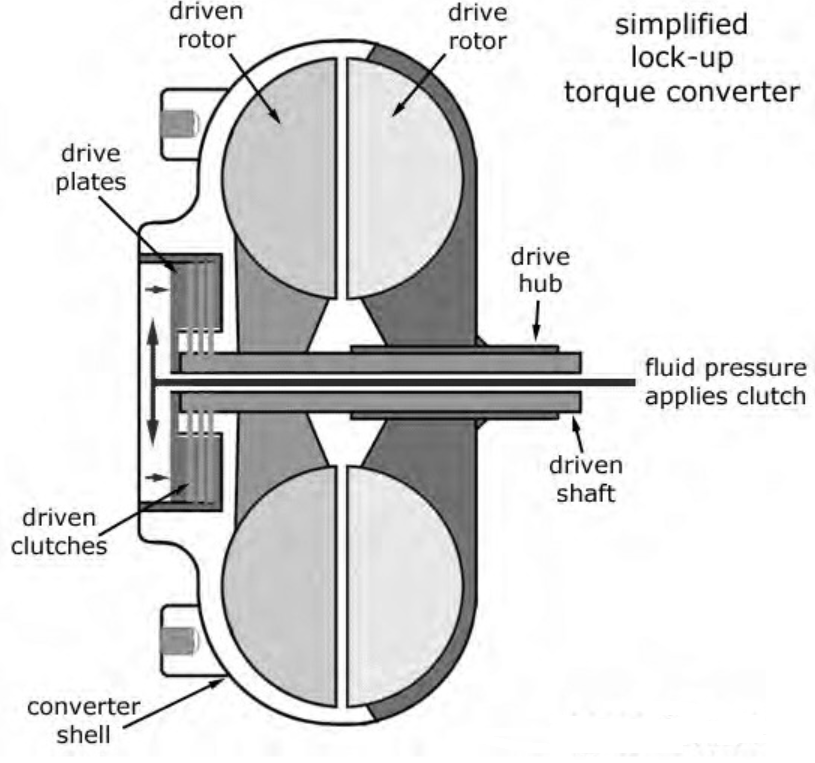
Instead of using air, the space inside the torque converter is normally full of an incompressible transmission fluid, which assists in transmitting the power generated from the engine to the transmission. Seems a bit odd, doesn’t it? Not exactly! The vehicle’s engine drives one of the turbines also known as the impeller that pushes the fluid onto the turbine. The torque converter is efficient since its blades are precisely engineered to maximize the energy transmission reducing heat build-up or turbulence.
(B) Operations inside a torque convertor
We can understand the insides of a torque converter by a simple example. Imagine having two fans facing each other. Turning on one of the fans will blow air over the blades of the second fan, causing it to spin as well. But if you are to hold the second fan still, the first fan will keep spinning nevertheless.
Parts of a torque convertor
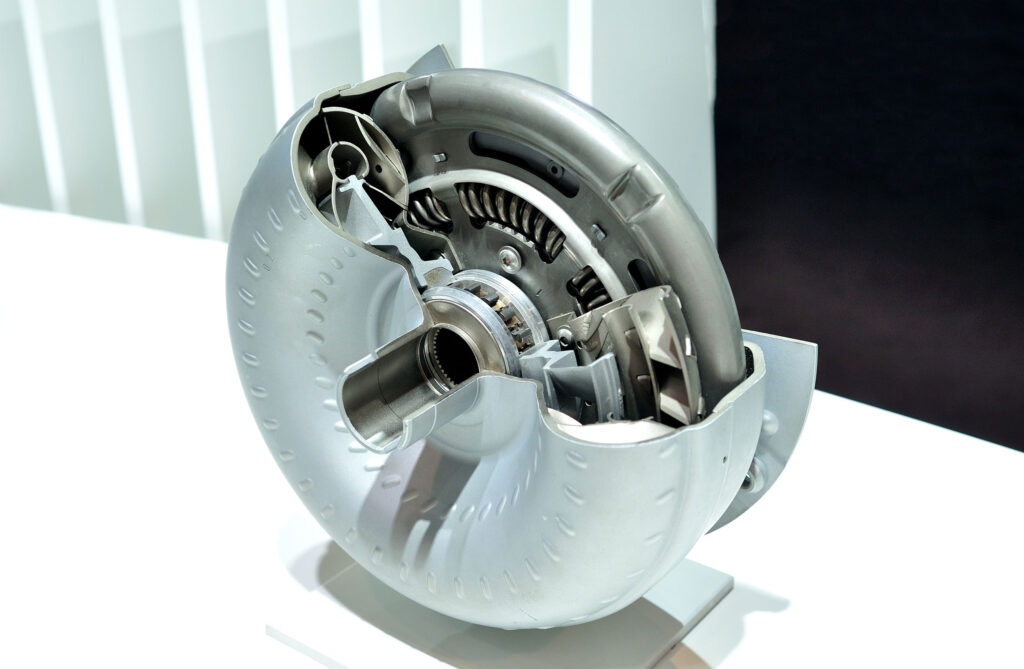
(A) Impeller
The impeller, also called a pump is filled up with fluid, which rotates with the engine crankshaft. This pump is a type of centrifugal pump. As it spins, it pushes fluid to the outside, just like the spin cycle of a washing machine pushes water and clothes to the outside of the washtub. As the transmission fluid is flung to the outside, a vacuum is created that draws more fluid in at the centre of the torque convertor. The more the spin rate, the more pressure is developed, which drives fluid in a faster way.
(B) Turbine
As the fluid from the impeller flows into the turbine, it spins the turbine blades. The spinning of the turbine causes the transmission to spin, which in turn moves your car. Since the flow of transmission fluid is a continuous process, the power is transferred from the outer to the inner section of the turbine, and then is turned back to the impeller. The movement of fluid from the impeller to the turbine develops a type of motion called coupling. Due to the curvature of the blades of the turbine, the fluid which enters the turbine from the outside, has to change direction before it exits the centre of the turbine. This directional change results in the spinning of the turbine.
(C) Stator
The stator is located at the centre of the device. It redirects the fluid returning from the turbine before it hits the pump again. This helps in increasing the efficiency of the torque converter dramatically. The stator comes into action after the fluid returns to the impeller. It is a different series of fins placed between the turbines on the transmission shaft. The blades of the stator are positioned in such a way that the fluid movement changes its direction and get directed back to the impeller. Therefore, when the vehicle breaks down, then the stator’s one-way clutch lets it stop spinning that disrupts the hydraulic connection.
Working
It’s not easy to understand the concept of how a fluid can provide the power to move something as significant as a car. A pump helps in achieving torque control that operates by sending fluid around the torque converter determined by the rotation of the crankshaft. Inside the housing of the device is a turbine that rotates as the pumped fluid comes into contact with the turbine blades, which helps monitor the amount of torque that gets to the transmission through the transmission shafts.
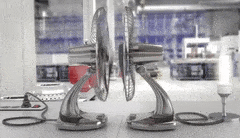
Within the housing of the turbine, the torque converter casing connects to the flywheel which spins at the same rate as the crankshaft. The impeller effectively pushes the transmission fluid into the blades of the turbine which in turn transmits the torque into the transmission. The stator acts as the barrier that flings the fluid back into the turbine instead of into the pump, hence increasing efficiency in the system.
The rate at which the transmission fluid pumps into the turbine is reduced while the car is idling, i.e. only a small amount of torque gets to the engine through the transmission. Fluid is propelled faster from the pump to the turbine as the crankshaft rotates faster with more throttles rotating the flywheel, hence forcing the turbine to rotate faster, which in turn allows for more torque to be transmitted through the transmission.
Advantages and Disadvantages
(A) Advantages of a torque convertor
- It allows a car with automatic transmission to stop without damaging its engine
- It provides your car with additional torque when you accelerate out of a stop.
- Modern torque converters have the capacity to multiply the torque of the engine by two to three folds.
(B) Disadvantages of a torque convertor
- Cars with automatic transmissions get worse gas mileage than cars with manual transmissions.
- This is because at higher speeds, the transmission speed catches up to that of the engine, hence eventually moving at almost equal speeds. This difference in speed wastes power.
Applications of Torque convertor
Due to its exceptional performance, the torque convertor is being utilized in many ways. Few of them are below:
- In marine propulsion systems.
- An amazing device for the automatic transmission.
- Utilization in the automotive industry for winches, drilling rigs, and conveyor drives.
- Used in the construction department for modern day forklifts, and railway locomotives.