Types of Gaskets: Metallic Gasket, Non Metallic Gasket & Composite Gasket
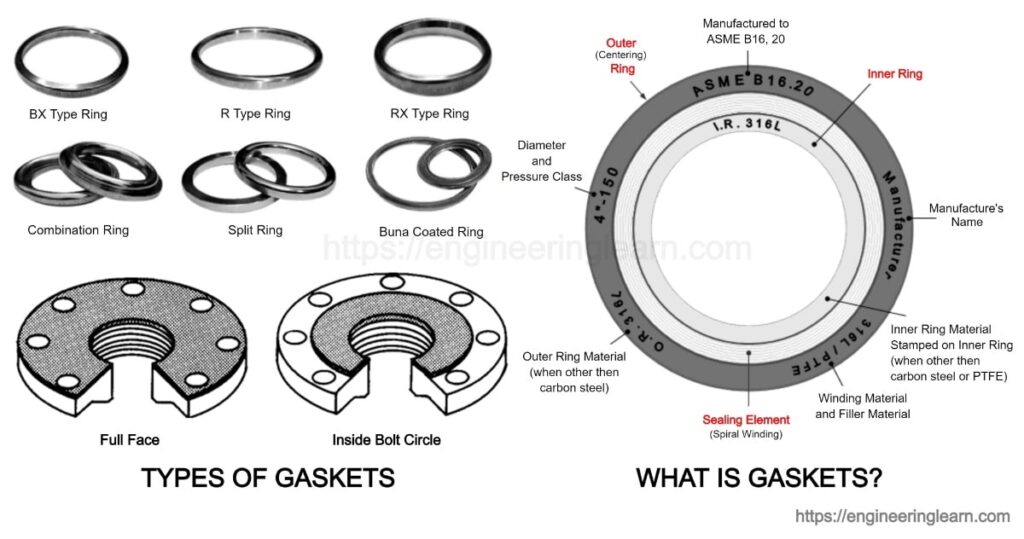
What is Gaskets?
Types of Gaskets: Metallic Gaskets, Non Metallic Gaskets & Composite Gasket :- The gaskets, sometimes also known as sealings, are the materials which are used to seal the two circular mating parts and make it leak proof. These are generally applied at the flanges of the mating pipelines of different fluids or pressure vessels to create a static seal and make it completely leak proof in all working as well as weather conditions.
Function of a Gasket
The main function of a gasket is to seal away any leaks between the two mating parts. For the purpose, a gasket must be compressed sufficiently to generate the barrier that will form a pressure tight seal and protect the inside fluids to leak out. Furthermore, a gasket also protects the moving parts of a mechanical system by preventing them from rubbing against hard surfaces and causing friction.
The Quality of a Gasket
The quality of a gasket is judged upon some parameters, which are shown below: –
1. Resilience
The mating parts or flanges of the assembly are generally stable. But, due to application of pressure and temperature the assembly starts vibrating or goes under fatigue condition. The gaskets should be resilient enough to tackle out such movement easily.
2. Corrosion Resistant
There may different kind of fluid that can flow through the assembly and comes into contact with the gasket. The gasket should be corrosion resistant to avoid corrosion not only for self but also to the flanges.
3. Creep Resistant
The gasket may subject to the high temperature application. At such high temperature gasket should not lose its strength over a period of time.
4. Compressibility
The gasket should be compressible so that it could retain the surface of the mating flanges and make it leak proof.
5. Impermeability
The gasket should be impermeable so that the fluid flowing through the application could not leak out through the gasket.
Types of Gaskets
There are, basically, three types of gaskets used to make the mating part of the container leak proof:-
1. Non metallic gasket
2. Metallic gasket
3. Composite gasket
1. Non Metallic Gasket: ( Types of Gaskets )
These are the most commonly used gaskets which are generally made up of rubber, graphite, polymers (such as Teflon, PTFE etc.), compressed non asbestos fibre (CNAF) etc. These kinds of gaskets are generally soft and can easily compress with the low tension bolting.
Some characteristics of non metallic gaskets: –
- Cheap and easily available.
- Rubber or elastomeric gaskets easily adapts the surface irregularities and seal it properly. But, these cannot be used in hydrocarbon services.
- Non metallic gaskets are used with the low pressure and low temperature flanges. However, the graphite gaskets can sustain its property up to temperature 500oC.
- ASME B 16.21 standard is used for the selection and configuration of non metallic gaskets.
The non metallic gaskets are of two types; full face type and inside bolt circle type. The full face gaskets are suitable for flat flanges and generally used for temporary connections in utility lines, whereas the inside bolt circle gaskets are suitable for the raised surface flanges and most of the time used for permanent connections.
2. Metallic Gasket: ( Types of Gaskets )
The metallic gaskets are also known as the ring gaskets. These gaskets are generally made of Soft iron, Babbitt metal, Low carbon steel, Super alloys, Monel etc.
Some characteristics of metallic gaskets: –
- Metallic gaskets are generally used for high pressure and high temperature flanges. The superalloys can sustain its strength up to temperature 1200oC.
- The metallic gaskets require high tension bolting for effective sealings.
- The metallic gaskets are very robust and generally costly.
- ASME B 16.20 standard is used for the selection and configuration of metallic gaskets.
The metallic gaskets generally fits into the groove made on the surface of the flange of the two mating parts. There are basically two kind of metallic gaskets are available; one is of octagonal type cross-section and another one is of ellipse (oval) type of cross-section.
3. Composite Gasket: ( Types of Gaskets )
The composite gasket is also known as semi metallic gasket because it is made of combination of metal and non metal. Different numbers of combinations can be done based on the requirement to produce the composite gaskets.
Some characteristics of Composite gaskets: –
- These gaskets can be used to a large variation of pressure and temperature.
- These gaskets are very cost effective if compared to the metal gasket. But, due to large brittleness property, it should be handled with care.
- The composite gaskets are generally used on raised face flanges, male-female type flanges and tongue & groove type flanges.
There are mainly three types of composite gaskets, which are well known to the technocrats; spiral wound gaskets, metal jacketed gaskets and cam profile gaskets.
1. Spiral wound gaskets
he spiral wound gaskets are the most widely used composite type gasket. These gaskets have good tolerance and recovery for flange surface irregularities. When the gasket is compressed the sealing is caused by the combined effect of metal and soft filler. These kinds of gaskets are used for the applications which are subjected to thermal or load fatigue stresses, shock or vibration.
There are three components of the spiral wound gaskets; Inner and outer ring, Filler material and winding material. Generally, the Teflon or graphite or aramid fiber is used as filler material whereas stainless steel is used as winding material. The inner and outer ring, made of metals, provides the required robustness for the application. The filler material provides the sealing effect and the winding material provides the resilience to the gasket.
The winding outer ring has V-type or W-type groove on the outer periphery, over this groove the filler and winding material are wound tightly assuring that it will not slip during the operation. The BS 3381 standard is used for the selection of spiral wound gaskets.
2. Metal jacketed gaskets
Instead of making layer by layer winding of soft and hard material like in spiral wounded gasket, the metal jacketed gasket encloses the soft filler material in a thin sheet of metal . The filler materials generally used are Teflon, aramid fibers etc. whereas to save the metal jacket from corrosion, stainless steel is generally used as jacket material. There are many ways to cover the soft material through the thin metal sheet.
3. Cam profile gaskets
In cam profile gaskets a corrugated profile metallic core, on both the surface, is used. Over this metallic core layer of soft sealing material such as graphite, PTFE etc. are settled. These types of configuration allow the cam profile gaskets to fit in moderate as well as extreme applications.
Selection of Gasket
Although there are different types of gaskets are available but the selection of gasket for the application is a tedious job. Any mismanagement may lead to disastrous result as leakage of poisonous fluid from the assembly may cause loss of lives and inventory. The selection of a gasket may be based on the following parameters:-
- Temperature: – The gaskets should be selected on the basis of their sustainable temperature range. The gasket should have to handle the temperature of the fluid that it contains.
- Pressure: – the gasket should be selected in such a way that it should handle the pressure of the fluid it contains during the operation.
- Resilient: – The gasket should be resilient enough to handle the vibration and load fluctuation during the operation.
- Type of fluid: – The gasket should be selected on the basis of type of fluid that will be in contact with the gasket. According to the fluid the corrosive resistant of the gasket material is determined and then the type of gasket should be chosen.
- Availability: – The gasket should be easily available in the market.
- Cost: – The gasket should be cheap enough for the required application.
- Service life: -The gasket should be chosen on basis of their life cycle in particular application.
There are some applications of the gaskets which are listed below:
- Heat exchangers
- Boilers
- Pressure vessels
- Oil & Gas pipelines
- Water pipelines etc.