Types of Extruders: Application & Working Principle
What is Extruder?
Types of Extruders: Application and Working Principle :- Extruders are one of the most important component which is used in the manufacturing process. Whenever these are combined with feeding, cutting, de-airing or other form of equipment it can create everything. There are various types of extruder machines about which one must know. So scroll down to learn more.
Types of Extruders
1. Single Screw Extruder & Twin Screw Extruder
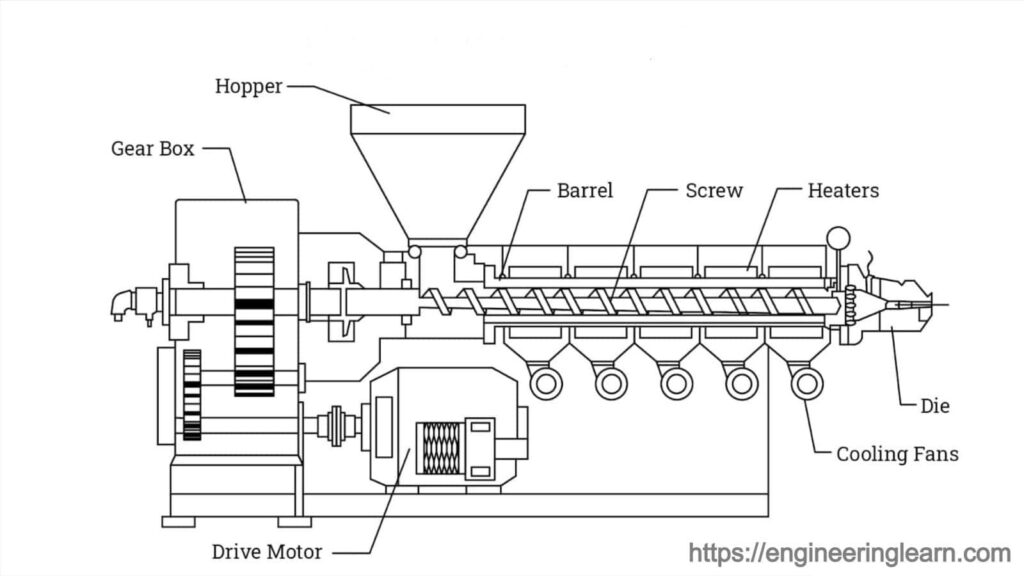
There are two types of extruders which are mostly know. First is the single and other is the twin screw extruder. Twin screw extruders are those which offer counter rotating. These come along with a very wide range of screw dimensions and designs. The single screw and the twin screw both are axially open-channel extruders as they can be regarded as the drag flow pumps.
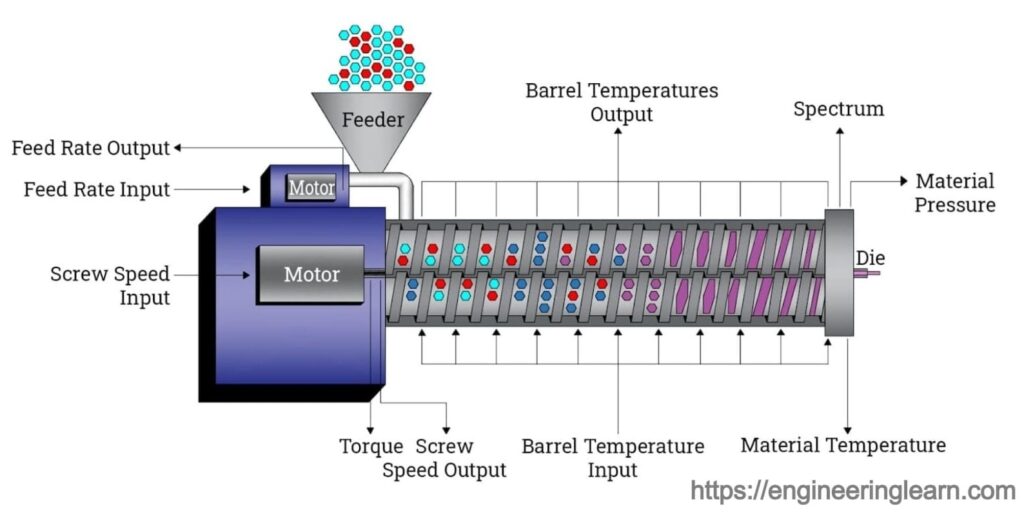
If the output or degree of fill is not found running at the maximum volumetric rate it can be impacted by the pressure flow within the extruder. The counter-rotating twin screw extruders are found forming a closed channel inside the intermeshing region as the output is less vulnerable as compared to the pressure flow within the extruder. They are considered to be having positive displacement pumps.
Function of Single Screw Extruder
The main function of the extruder is to convert the solid plastic into a uniform melt by the effect of heating, pressurizing and shearing after which it is send to the next process. The procedure of melting involves processes like mixing color, master-batches, blending resins and re-grinding. The finishing should mandatorily be done uniformly in concentration and temperature. The effect of pressure must be large enough in order to squeeze the viscous polymer.
The extruder is responsible for performing all of the above processes with a barrel, screw and a spiral knife. The plastic pellets get in to the barrel via hopper which is placed at one end of the barrel and then are passed through the screw to the other end of the barrel. For maintaining the pressure, the depth of the threads on the screw is decreased as the hopper keeps on increasing.
Principle of Twin-Screw Plastic Extruder
The twin-screw extruder works on a principle of an extruder for a single-screw extruder wherein the process like transport, melting, pressurization, pumping, mixing, stripping and de-volatilization are all conducted due to these extruders. A recent research on the twin-screw extrusion theory stated the complexity of the screw’s geometry and the process of extrusion was also found to be very complicated which brought many difficulties in the research.
2. Rubber Extruders: ( Types of Extruders )
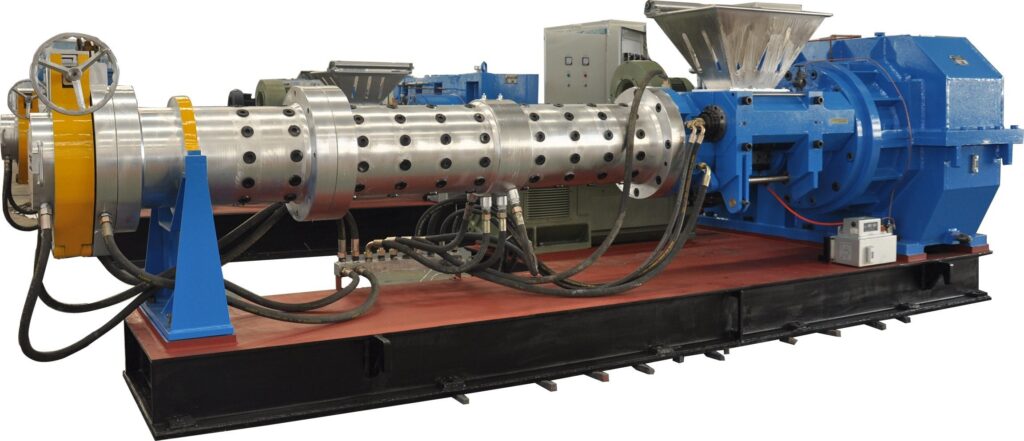
The manufacturers who deal with the material like rubber bales, silicone and EPDM are aware that breaking them is the hardest thing which anyone can do. These are the materials which generally come in large quantities due to their stickiness and also require a very special chemical or talc which needs to be formed into manageable sizes and consistencies.
After the collaboration with the some of the companies, the custom extruders were designed specifically for the machines according to their sizes and the manufacturing needs were improved and controlled. In case there are any tight space constraints, then there are compact solutions to meet the site requirement.
3. Food Extruders: ( Types of Extruders )
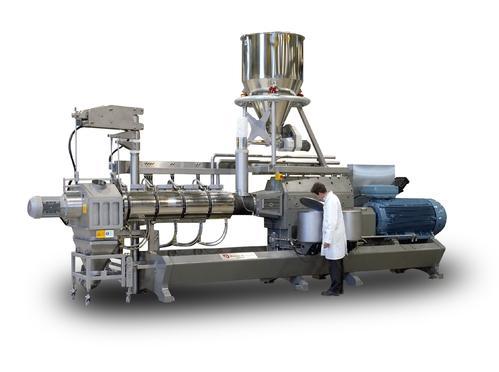
In the food industries, it is essential to have a high volume of consistent products which is created with the appropriate safety and efficiency standards. The types of extruders are designed for cooking and cooling food which has helped the food production process in various ways. For instance, a food extruder machines eliminates batch cooking by consistently cooking semi-moist, moist, dry and pre-mixed foods with a high temperature, pressure and timing precision.
Once it is combined with a custom extrusion dies and extrusion cutters, the same unit is used to create an unlimited variety of food pellet in varying shapes and sizes. In terms of safety and longevity, the food extruders are made with the material stainless steel in order to ensure the sanitary production and less downtime for replacing the parts.
4. Lab Extruders: ( Types of Extruders )
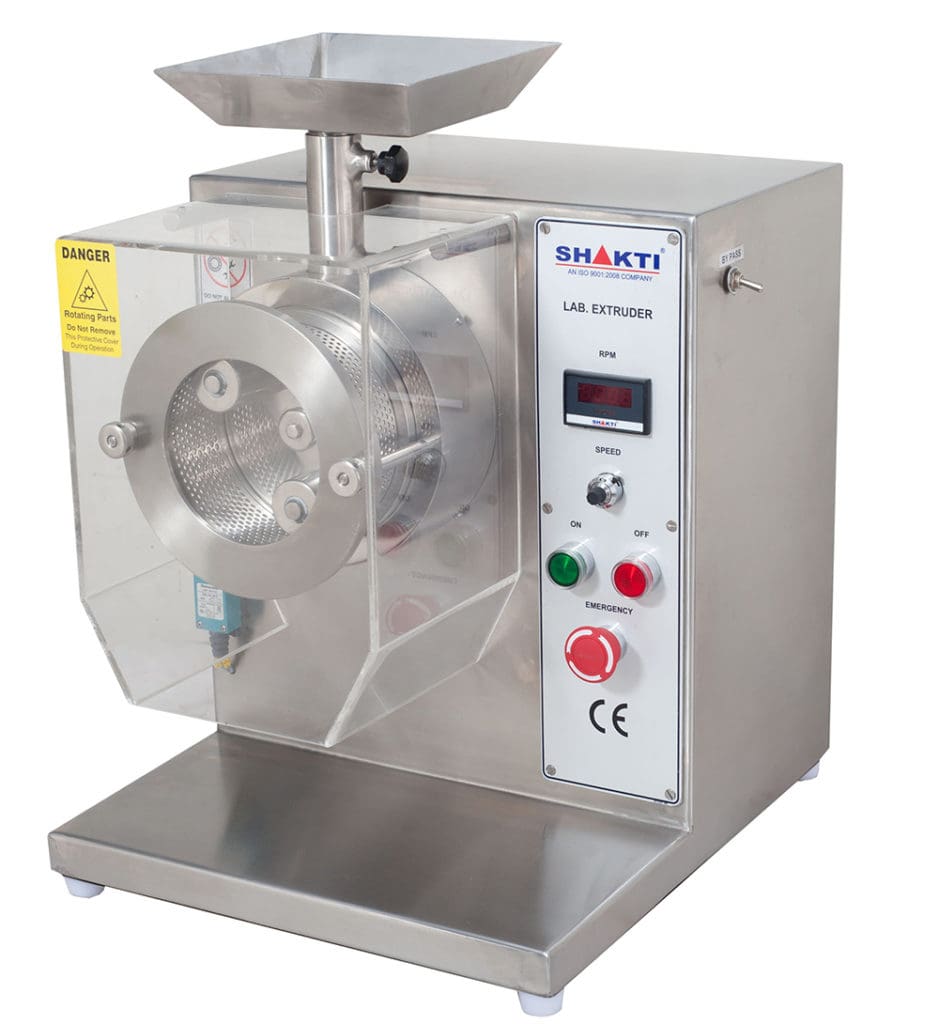
There are various types of extruder units which are in the need of production in small batches of materials, like in the testing departments across the industries. These type of extruders are quite small in dimension and are found to be table mounted in order to meet the needs of any lab space or facility layout.
The lab extruders are mostly used in creating the activated carbon for air and water purification. These are found having a wide range of part shapes and sizes which includes auger, barrel, screw and die configurations. Depending on the need of constructing it in different materials like stainless steel or carbon steel is available. The potential for customization in lab extruders is almost limitless.
5. Catalyst Extruders: ( Types of Extruders )
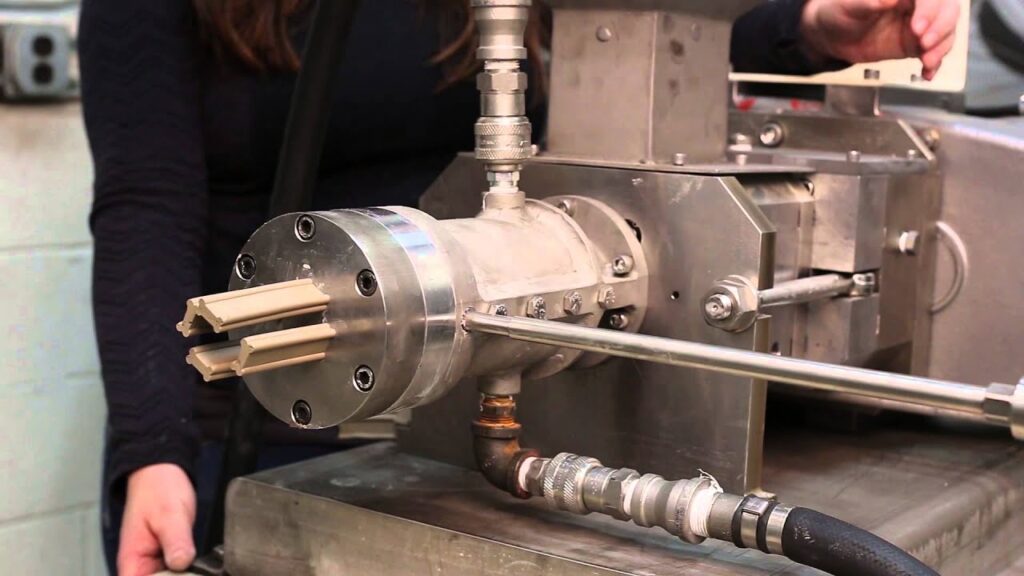
The catalyst extruders are used from refining crude materials to changing its molecular structure, as catalysts are found to be a very crucial part of a production process. The types of extruders which are used in the catalyst industry are unmatched in their level of customization. The extruder models are available in various bench-top sizes whereas the standard sizes are 4″, 6″ and 8″ sizes for high volume production.
Jacketed barrels are also designed for a specified level of heating or cooling requirement, along with the custom auger and barrel dimensions. The level of customization in the final product will help in sustaining the operational requirements in order to meet the exceeded peak load specifications.