Pinch Valve: Types, Function, Components, Working Principle, Applications, Advantages & Limitations
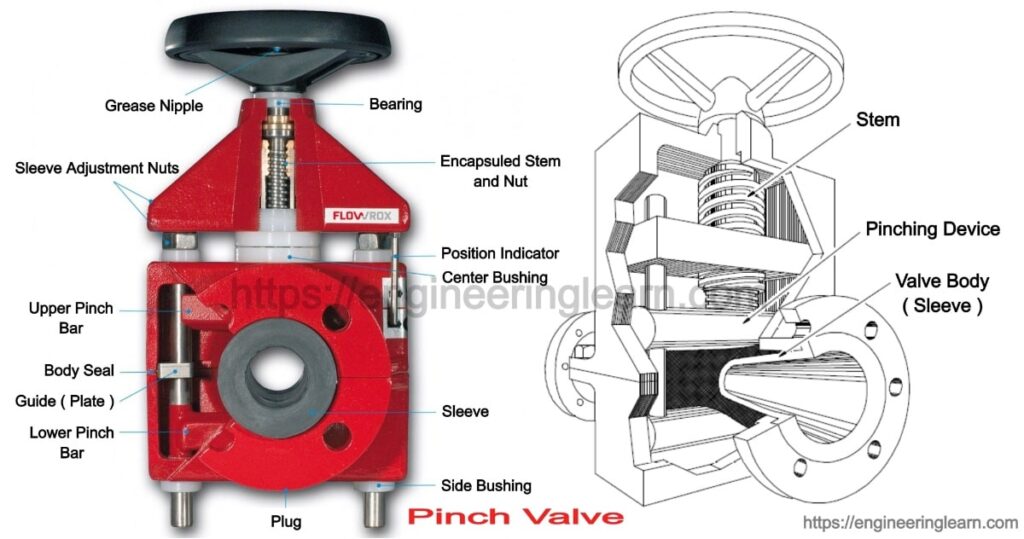
What is a Pinch Valve?
Pinch Valve: Types, Function, Components, Working Principle, Applications, Advantages & Limitations :- The pinch valve or sometimes called squeeze valve is a flow control valve which operates on the squeezing action of rubber sleeve inside the valve. The valve is opened or closed by compressed air, which squeezes the rubber sleeve and controls the passage area. The valve has no constraints in the open position, allowing a wide range of media to pass through the bore. The valve’s flexible interior rubber sleeve isolates the medium, reducing the danger of contamination.
Significance of Pinch Valves
Pinch valves are ideal for segregating and controlling abrasive, corrosive, and fibrous materials. For emulsions, sludges, dusts, gaseous materials, compressed air, powder, granulates, and pellets, the pinch valve is extensively being applied as an isolating or regulating valve. These valves are inexpensive, durable, and simple to operate, making them ideal for a variety of industrial applications.
Pinch Valve Components and Working Principle
A pinch valve is made up of three main parts: housing, an internal rubber sleeve and end connections. The rubber sleeve is the only component that comes into contact with the media and is inserted into the housing from input to output. To give support and connection to the valve, the end connectors are fastened, screwed, or threaded at both of the end. When compressed air is delivered to the valve, it pushes the rubber sleeve down. The flow is stopped and the valve is closed when the rubber sleeve is entirely pinched. Unlike traditional valves such as ball Valve or gate valve, which can trap particles around the ball or discs, the rubber sleeve of a pinch valve can capture particles around it, resulting in an excellent shut off.
The elastic rebounding property of the rubber sleeve, combined with the force of the flowing media, fully opens the valve when the external air pressure is no longer applicable. The flowing media is only in contact with the rubber sleeve, which consequently isolates the media, prevents contamination, and prevents damage to other parts. The rubber sleeve absorbs the impact of the flowing media and deflects it back when it strikes it. This robust feature allows the rubber sleeve to wear at a somewhat slower pace than metal surfaces, resulting in a longer service life.
Types of Pinch Valves
The pinch valves are generally of three types; normally open (NO) pinch valve, Normally close (NC) pinch valve and Changeover (CO) pinch valve. However, NO type pinch valves are used commonly to incorporate the flow control but according to the use and fluid control the different pinch valves are introduced in the system.
1. Normally Open (NO) Pinch Valve
These valves are in open condition at the non-pressurized state (normal state). To close the valve the pressurized air is inserted over the rubber sleeve to induce the pinching effect. These valves actuates on two kind of pressure forces; operating pressure (fluid pressure) force and positive control pressure (air pressure) force.
2. Normally Closed (NC) Pinch Valve
These valves are generally closed at the non pressurized state. The closing operation is performed by the spring element which forces the pinch element to be closed at normal conditions. As the negative pressure (vacuum pressure) is applied at the air vent of the valve and exceeds the spring force, the rubber sleeve opens the passage and the flow starts. The actuation of the sleeve is done by the spring force, operating pressure force and control pressure force.
3. Changeover (CO) Pinch Valve
The CO type valve incorporates dual channel operation, which means its half part is made No type and another half is made NC type. The changeover between the NO and NC type can be done anytime by sliding the changeover nut. The actuating forces include in the operation of this valve is spring force, operating pressure force and control pressure force.