Types of Rubber Molding
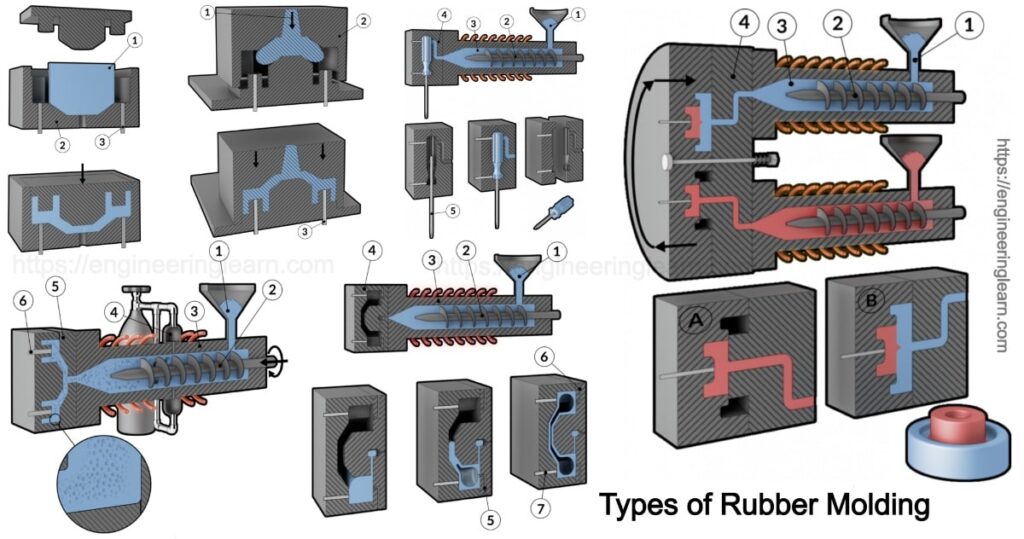
Types of Rubber Molding :- primary purpose of molding is to provide shape & size of the product. Porosity and knit are terms that to be avoided. Porosity caused by presence of moisture in the compound & knit by the improper flow of feed. Molding is used to developed the compound to meet the requirements as per product quality. Molding process basically depend upon three factors are:
- Compound characteristics
- Mooney viscosity
- scorch characteristics.
TYPES OF MOLDING :-
There are mainly 3 types of molding are described below:
- Compression molding
- Injection molding
- Transfer molding
1. Compression Molding
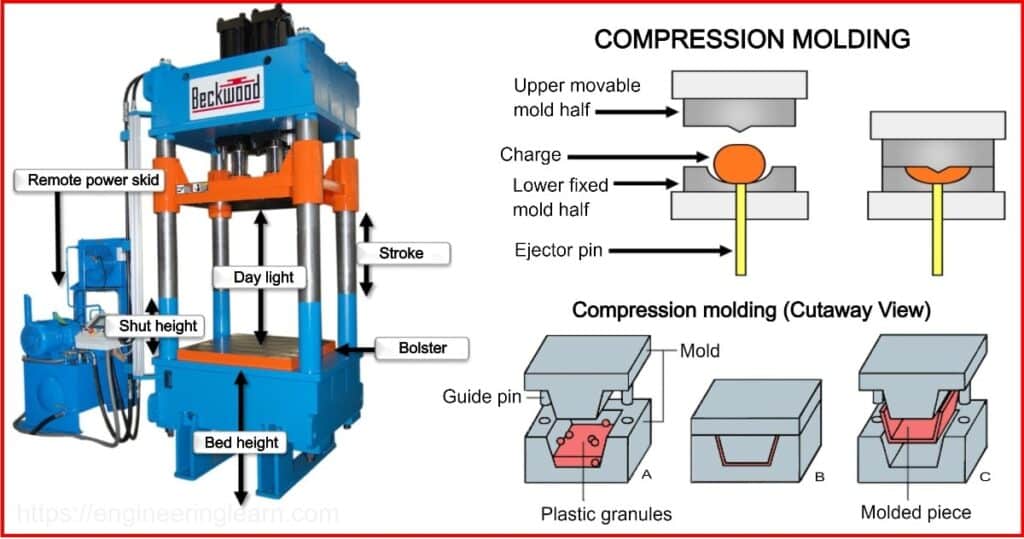
compression molding involves requirement of blank ( of required shape, size, weight). Plays important role to control flow rate of mold to avoid air entrapment into that includes excess flash.
Compression molding includes : open mold with elastomer blank paced in the cavity. Closed mold forming the final output consumable product.
2. Injection Molding
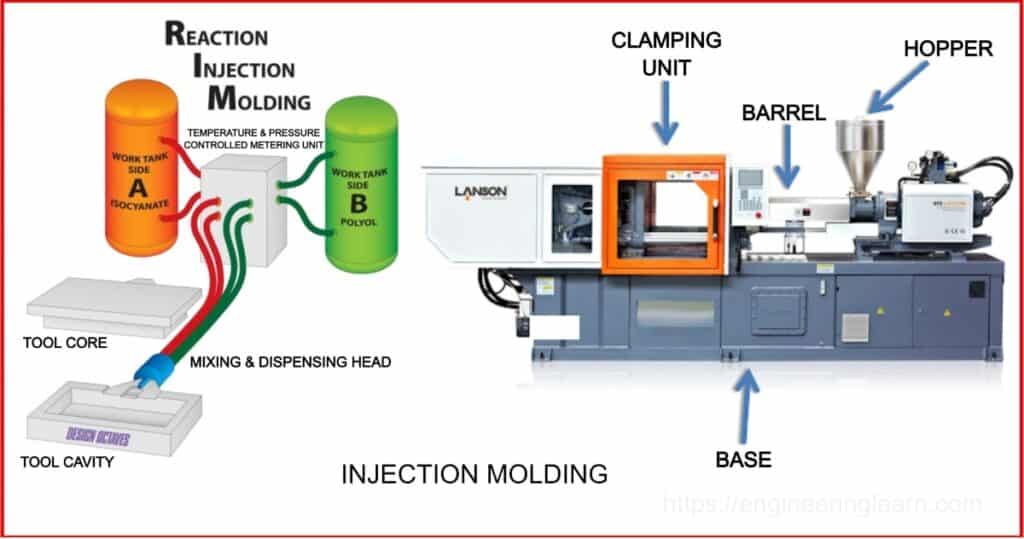
Injection molding is an important process that is used to convert elastomeric materials into finished products. Injection molding machine performs automatically which involves basics steps are:
- Raw material feeding
- Heating
- Polymer mix plasticization
- And finally the mold injection.
All of the above described steps are based on their controllable condition of temperature, pressure, time, speed.
Injection molding involves rubber compounds are subjected under high stress rate. There is thermal history of leading to chemical reaction. Different rubber compound shows their different chemo- rheological behavior and properties too.
Types of injection molding machines
- The toggle or hydraulic mold closing mechanism.
- Plunger types or screw type plasticization unit or injection unit.
Operation principles
- Injection forming
- Conventional
- Transfer – injection molding methods
3. Compression and transfer molding
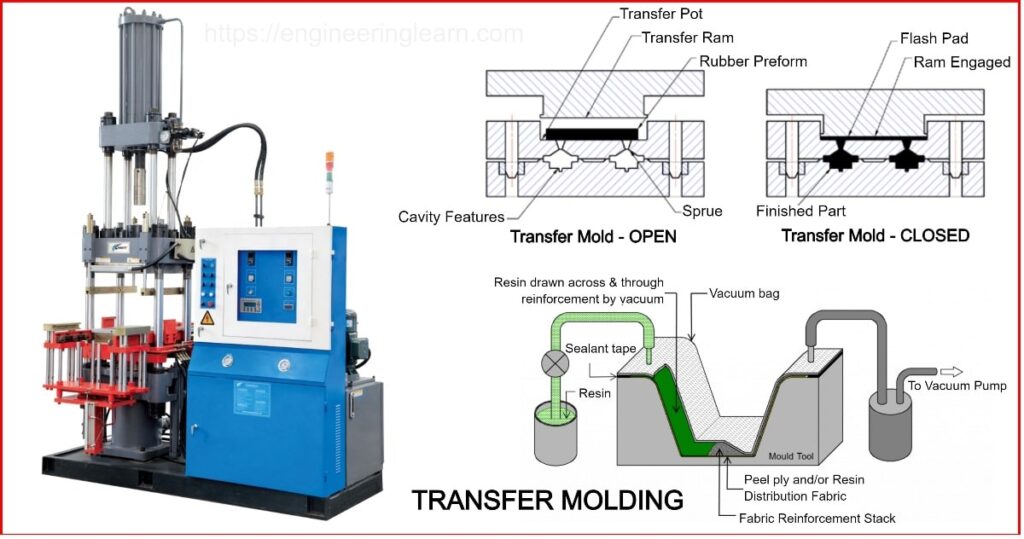
Elastomers is pushed into the mold cavity as the mold closes. Therefore in feed elastomer comes in contact with hot surface of mold (maintaing high temperature) without any imposed pressure( exception some pressure that is created when mold face is about to close). For vulcanization both pressure and temperature are required.
Injection molding
in this molding the mold closes firstly then elastomer is pushed into mold which is operating at high speed. Pressure is developed in very short interval of time as the elastomer is filled quickly in mold face, thereby trigging the process by vulcanization.
Advantages of rubber injection molding
- Automation (electrical scope) is introduced during the moulding operation.
- Simplifies preparation of rubber: cutting, shaping & weighing of blanks and eliminated.
- Cure times reduced to 1/10th teeth or less compared with compression moulding.
- Materials, trimming and inspection price reduced ( economical).
Product quality improved: providing better control on dimension and more uniform physical properties.
Disadvantages of rubber injection molding
While there are many benefits of using the rubber injection moulding, as with most manufacturing processes, there are some disadvantages:
- Increased setup costs
- Restrictions on the design of the tool and ultimately the finished part
- The requirement of more expensive tooling and machinery.